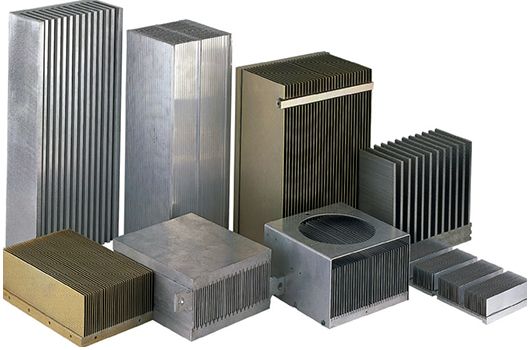
Bonded Fin Heat Sink Manufacturing Process
The principle of bonded fin heat sink technology is to use high thermal conductivity epoxy resin to bond and weld, and combine the fin and the base.
Advantages of Bonded Fin Heat Sink
- The aspect ratio of the fins and the high fin density increase the cooling surface area, so the heat sink has high performance.
- Heat sink fin material, copper or aluminum is optional.
- The heat sink fin is matched with a bonded base plate, copper base plate or aluminum base plate is optional.
- It can be designed according to customer's requirements. After the heat sink fin is made, it can be cut into a specific size.
- For high power forced convection cooling applications.
- Adhesive resin with high thermal conductivity to minimize thermal loss.
- Flexible production, both large and small heat sinks can be used.
The Main Application Range of Bonded Fin Heat Sink
IGBT devices, welding equipment, electrical equipment, high-power semiconductors, laser systems, renewable energy, factory automation, thermoelectric modules-TEC, uninterruptible power supply systems, AC welding switches, power rectification equipment, power rectification equipment.
Traction Control Motor Drive Cooling Industry: Large heat sinks.
Bonded Fin Heat Sink Production
- Prepare the aluminum / copper base and heat sink according to the design drawings, and make the grooved base.
- Heat sink and base are connected together with epoxy resin.
- Machining and surface treatment on the base and fins to form a bonded fin heat sink.
- Appearance surface treatment.
- Gallery