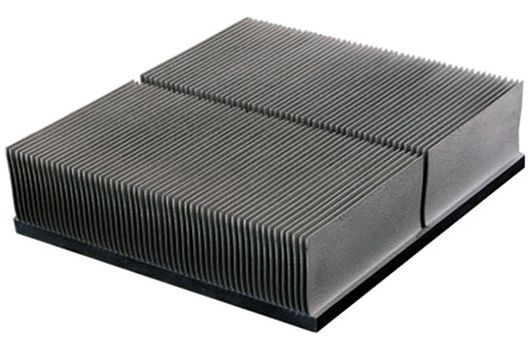
Skived Fin Heat Sink Manufacturing Process
The principle of skived fin heat sink is to use a single piece of material (such as copper or aluminum), and use a dedicated shoveling machine to cut high-density high-fin heat sinks with high-precision radiator shoveling technology
Skived fin heat sink overcomes the limitation of traditional heat sink thickness and length ratio (extruded type), and can produce high-density heat sink.
Due to the high purity of the intact material, there are no other joints, and this conduction efficiency is better than conventional heat sinks.
Advantages of Skived Fin Heat Sink Manufacturing Process
- High density and thin fins can produce fin density that cannot be achieved by extruded heat sinks.
- Manufacture does not require expensive molds, thus reducing mold costs.
- The skived fin structure is made of copper or aluminum in one piece, while the extruded type can only choose aluminum.
- There is no media connection between the heat sink and the base, which improves thermal performance compared to traditional heat sinks.
The Main Application Range of Skived Fin Heat Sink
IGBT devices, welding equipment, electrical equipment, high-power semiconductors, laser systems, renewable energy, factory automation, thermoelectric modules-TEC, uninterruptible power supply systems, AC welding switches, power rectification equipment, power rectification equipment.
Traction Control Motor Drive Cooling Industry: Large heat sinks.
Skived Fin Heat Sink Production
- Prepare aluminum / copper according to design drawings.
- High-precision cutting of radiator teeth.
- The bottom surface of the heat sink is polished and so on.
- Appearance surface treatment.
- Gallery
- Video