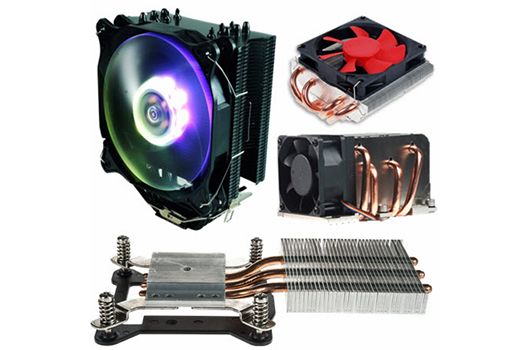
Stacked Fin Manufacturing Process
The principle of the stacked fin heat sink (Stacked Fin Assembly) uses the high-efficiency conduction efficiency of the copper heat pipe and the copper block as the center contact of the heat source, and then guides the heat source to the aluminum alloy for diffusion and heat dissipation.
It is mainly divided into two categories: the first type (bottom plate) uses aluminum alloy molding to design grooves and uses pressing methods to fix copper blocks or heat pipes; (heat sink) aluminum plates and heat pipes are pressed together for stacking and forming. This method can effectively increase the heat transfer efficiency and improve the performance of the heat sink.
The second type uses adhesives and welding to ensure that the aluminum alloy and the heat pipe or copper block can be tightly combined to improve heat dissipation efficiency.
Advantages of Stacked Fin Manufacturing Process
- Effectively increase the heat transfer efficiency and improve the performance of the heat sink.
- Utilize the fast conduction of copper and combine with the lightweight characteristics of aluminum.
- Adhesive-free stacking radiators, with environmental protection, cost saving and other benefits.
- The heat pipe radiator can effectively transfer the heat source to other areas, and the conduction direction can be controlled.
The Main Application Range of Stacked Fin Manufacturing Process
IGBT devices, welding equipment, electrical equipment, high-power semiconductors, laser systems, renewable energy, factory automation, thermoelectric modules-TEC, uninterruptible power supply systems, AC welding switches, power rectification equipment, power rectification equipment.
Traction Control Motor Drive Cooling Industry: Large heat sinks.
Stacked Fin Production Process
- Discuss the production process method according to the design drawings (combination of two processing methods).
- Design and manufacture of molds (base plate extrusion mold/fin stamping mold, etc.).
- Production and processing.
- Finished product packaging.
- Gallery